Emergency Preparedness on the Job Site
Nature isn’t always kind to industrial jobsites. In fact, it can often be downright ugly. High winds, floods, fires, earthquakes, and tornadoes are just some of the natural disasters that can ruin a project. But, disasters can also be manmade. Examples of manmade disasters include toxic gas releases, chemical spills, and explosions.
Whether natural or manmade, disasters disrupt operations and put workers at risk. They can also have a huge financial impact on a business. That’s why emergency preparedness at work is key. Having an emergency plan in place lets workers know where to go and what to do when a disaster strikes. It also helps reduce the panic and confusion that occurs when a disaster hits. This allows everyone at a jobsite to think more clearly and respond in a logical manner.
What Is Emergency Preparedness at Work?
An emergency preparedness plan enables a business to determine the best course of action to deal with worst-case scenarios. The plan encompasses steps that a company can take to keep its employees safe. And, it defines roles for employees, ensuring appropriate actions are performed to manage risk.
When it comes to emergency preparedness at work, it pays to err on the side of caution. This is especially true for businesses that have aerial lift operators on staff. Because, if an emergency strikes, aerial lift operators must be able to guard against tip-overs and other accidents.
Put Together an Emergency Preparedness Plan at Work
A business must develop and maintain an emergency preparedness plan at work. With this plan in place, a company can verify that it can handle any emergencies that occur, regardless of when they happen.
Ultimately, an emergency action plan outlines the actions employers and workers should take during fires and other emergencies. OSHA requires some employers to establish an emergency safety plan. These include companies that work with hazardous waste, toxic chemicals, and grain-handling facilities. Other companies are not required to have a plan. Even so, it’s always a good idea to have one as it helps protect your workers and your business.
Now, let’s look at what you can do to craft and maintain an effective plan for emergency preparedness at work.
Identify potential disasters.
In order to prescribe proper safety measures, you first have to know what could happen. Is the area where you work prone to weather disasters, such as earthquakes, flooding or tornadoes? Does your business involve working with toxic chemicals or hazardous materials? Is the landscape in a high fire-risk area? Make a list of all possible disasters, even those with a small chance of happening. From here, you can establish emergency preparedness at work priorities.
Prepare for the worst.
Next, create worst-case scenarios involving the disasters that could befall your business. If a tornado hit the jobsite, how much damage would it cause? If you suffered a toxic spill, how far would the danger zone extend? If a fire started, could it create other risks, such as explosions or lethal fumes. What are the worst injuries that could result from the disaster? Consider the worst-case scenarios, no matter how difficult it may be to do so. That way, you can ensure you’re prepared for any emergencies that come your way.
Establish an Emergency Plan
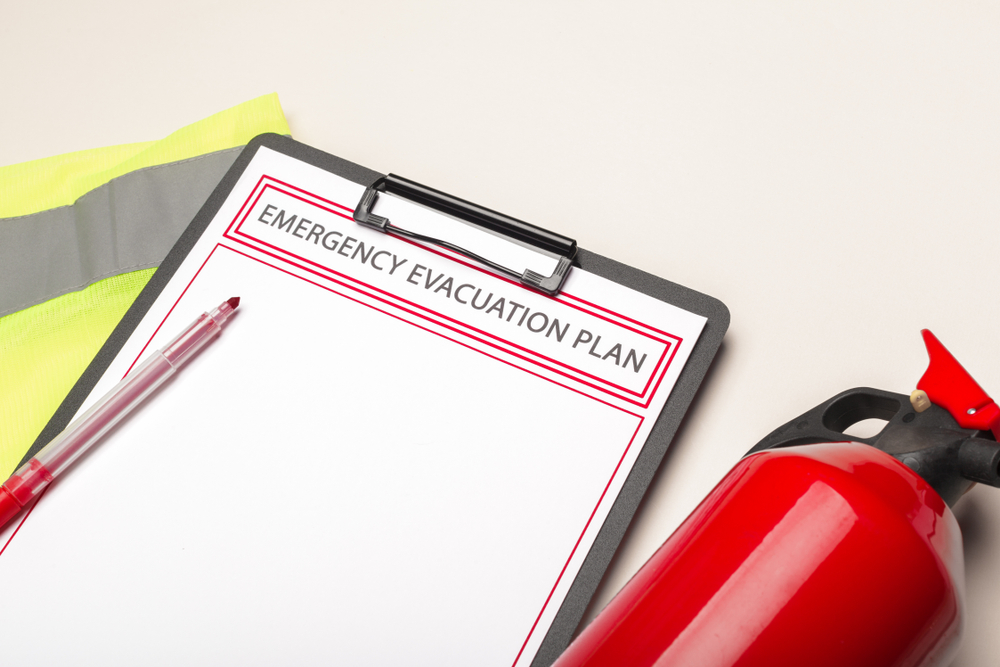
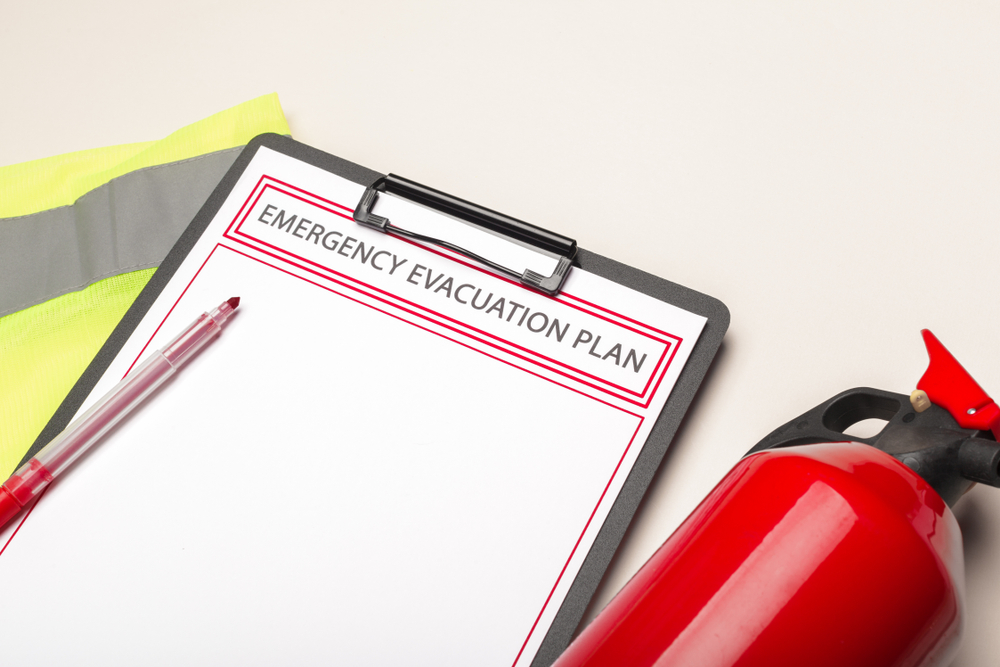
Now that you know what disasters could happen, the next step is to create an action plan to deal with them. The plan should:
-Assign actions and responsibilities to the right people
-Identify the lines of communication
-Provide guidelines for evacuation
-Identify safety measures for those who can’t evacuate
To get a complete picture of what could occur and how to respond to it, managers and workers should contribute during the planning phase. Together, both groups can identify what it takes to keep everyone safe at all stages of an emergency.
Train the troops.
There’s a reason schools and hospitals practice fire drills. Even though the fire isn’t real, it lets people practice what to do when it is. On the job site, workers should be trained on how to use emergency equipment. They should also know when and where to evacuate the site. For example, if people work on aerial lifts, they should know how to get down quickly. Practicing safety procedures is important because people are calmer when they know what to do. The higher the risk of a disaster, the more often you should practice the drills.
Protect your data.
Employee safety always comes first. But don’t forget to safeguard your data. Industrial companies must keep volumes of data regarding plans, projects, permits, equipment, employees and much more. Some of this is in paper form. Some is in electronic form. Both types can be easily destroyed in a disaster.
To protect it, make a list of all the places you store critical data and back it up. If it’s paper, make copies and store in a different location. If it’s digital, make regular backups; at least once a week. Store the backups in a different location than your computer servers. These days, the easiest way to back up data is through a cloud service.
Have ample insurance coverage.
Industrial companies should have three types of loss prevention coverage:
• Liability – In case employees or citizens get injured
• Property damage – In case your project and/or equipment get destroyed
• Negligence – To protect against lawsuits resulting from damage and/or injuries due to faulty work
Insurance can be expensive, but you can shop around for coverage. It often helps to discuss your business insurance requirements with insurance professionals. This allows you to ask questions regarding the different types of insurance, how they work, and their respective benefits. It also helps you get the appropriate coverage to ensure your business is protected if an emergency occurs.
Remember, the cost of insurance is minimal compared to the damages you might have to pay from a major lawsuit. So, make sure your business is covered to the largest amount possible.
Keep your emergency plan up to date.
Things change quickly in today’s world. New projects, new employees, new equipment – all present good reasons to review and update your disaster preparedness plan.
Disasters often happen when we least expect it. Being prepared when it occurs can help minimize damage to your employees and equipment. And, it can hopefully prevent the loss of life.
Construction Emergency Preparedness Plan: What Is It, and Why Is It Important?
If you run a construction business, you need an emergency preparedness plan that accounts for cave-ins, fall arrest rescues, and other life-threatening situations. The plan requires your business to consider a variety of emergency factors, such as:
- Administration of basic first aid
- Evacuation and exit procedures and routes
- Alarm systems
- Reporting
Your construction workers must be prepared for emergencies, too. As such, you should provide your workers with sufficient emergency preparedness training. At this time, you can also offer aerial lift safety training, so your workers can operate lifts in accordance with OSHA standards.
Give Your Workers OSHA-Compliant Aerial Lift Safety Training
Aerial lift safety and emergency preparedness training can go hand in hand. Both empower workers to do their part to limit risk across jobsites. Plus, they can help workers stop emergencies before they harm workers and employers.
CertifyMeOnline.net makes it simple to provide OSHA-approved aerial lift safety training to your workers. With our help, you can get your workers in compliance with OSHA aerial lift safety mandates in as little as one hour.
To learn more about our aerial lift safety training program or to enroll your workers in it, please contact us online or call us today at (602) 277-0615.